Ensuring Safety and Quality in Industry
In the industrial world, ensuring the integrity and safety of materials and components is crucial. Advanced inspection techniques are employed to detect flaws that might be invisible to the naked eye. Among these, techniques involving magnetics and dyes are particularly effective for inspecting various types of materials. This exploration will delve into the realm of industrial inspection techniques, shedding light on the significance and application of magnetic particle inspection and dye penetrant testing in upholding rigorous safety and quality standards.
Magnetic Particle Inspection: Unveiling Surface and Subsurface Anomalies
Magnetic particle inspection (MPI) is a non-destructive testing method used to detect surface and subsurface discontinuities in ferromagnetic materials. This technique involves magnetizing the material and then applying ferromagnetic particles to the surface. The presence of a flaw will distort the magnetic field and attract the particles, forming a visible indication on the material’s surface.

The Process of Magnetic Particle Inspection
MPI can be conducted using either dry or wet ferromagnetic particles, depending on the specific requirements of the inspection. The process includes several steps:
- Surface Preparation: The material’s surface is cleaned to remove any contaminants that might interfere with the test.
- Magnetization: The material is magnetized using direct or indirect magnetization methods.
- Application of Particles: Magnetic particles are applied over the surface.
- Inspection: The inspector examines the material under proper lighting to identify any particle accumulations that indicate flaws.
- Demagnetization: After inspection, the material is demagnetized to remove any residual magnetic field.
Advantages of Magnetic Particle Inspection
- High Sensitivity: MPI can detect both surface and slightly subsurface discontinuities.
- Immediate Results: The indications of flaws are visible immediately after the application of particles.
- Versatility: This method can be used on a variety of ferromagnetic materials.
Limitations of Magnetic Particle Inspection
- Material Limitation: MPI is only applicable to ferromagnetic materials.
- Surface Accessibility: The entire surface to be inspected must be accessible.
- Skill Requirement: The technique requires skilled personnel to interpret the results accurately.
Dye Penetrant Inspection: Revealing Hidden Cracks
Dye penetrant inspection, also known as liquid penetrant testing, is a widely used non-destructive testing method to locate surface-breaking defects in all non-porous materials. This method involves applying a liquid with high surface wetting characteristics to the surface of the test material.
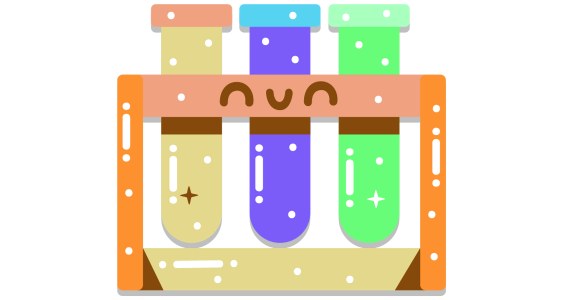
Conducting Dye Penetrant Inspection
The process of dye penetrant testing typically involves the following steps:
- Cleaning: The surface of the material is thoroughly cleaned to remove any dirt or grease.
- Application of Penetrant: A dye penetrant is applied over the surface.
- Dwell Time: The penetrant is left on the surface for a specific period to allow penetration into any flaws.
- Removal of Excess Penetrant: The excess penetrant is carefully cleaned off the surface.
- Developer Application: A developer is applied, which helps draw out the penetrant from any flaws to create a visible indication.
- Inspection: The inspector examines the material for any indications of defects.
Advantages of Dye Penetrant Inspection
- Applicability to Various Materials: It can be used on a wide range of non-porous materials.
- Sensitivity to Small Defects: Highly effective in revealing small surface-breaking flaws.
- Simple Process: The process is relatively simple and does not require highly specialized equipment.
Limitations of Dye Penetrant Inspection
- Surface-Breaking Defects Only: It can only detect flaws that break the surface.
- Surface Preparation: The surface must be thoroughly cleaned for effective results.
- Post-Cleaning Requirement: The material needs proper cleaning after inspection to remove residues.
Choosing the Right Industrial Inspection Techniques
The choice between magnetic particle and dye penetrant inspection depends on the material type and the nature of the expected flaws. MPI is ideal for ferromagnetic materials with potential subsurface flaws, while dye penetrant testing is suitable for a wide range of materials where surface-breaking flaws are of concern.
Technological Advancements in Inspection Techniques
Technological advancements have enhanced both magnetic particle and dye penetrant inspections. Automated systems and improved materials have made these techniques more efficient and reliable.
Training and Certification for Inspectors
Proper training and certification are essential for inspectors conducting these tests. Understanding the principles, techniques, and limitations ensures accurate and reliable inspection results.
Ensuring Integrity through Advanced Inspection
Magnetic particle and dye penetrant inspections are indispensable in the industrial sector for ensuring the integrity and safety of materials. By understanding and properly applying these techniques, industries can prevent failures, maintain quality, and uphold safety standards.
Whether it’s the complex geometry of a machine component or the critical parts of a structure, these inspection methods stand as pillars of quality assurance in the manufacturing and construction industries.
See Also: How a SIM Card for Europe Enhances Your Travel Experience