In the intricate world of modern engineering and product design, a myriad of challenges often arise, requiring innovative solutions to ensure optimal functionality and performance. From space constraints and environmental hazards to specific electrical requirements, engineers and designers are constantly seeking ways to overcome these hurdles and bring their visions to life. Custom cable assemblies have emerged as a critical tool in addressing these challenges, offering tailor-made solutions that meet the precise needs of any project.
Understanding Custom Cable Assemblies
Custom cable assemblies, in essence, are pre-assembled cables and connectors designed and manufactured to meet specific requirements. Unlike off-the-shelf cables, which may offer limited flexibility and compatibility, custom assemblies provide a perfect fit for unique applications. These assemblies can incorporate a wide array of components, including wires, connectors, shielding, and overmolding, each carefully selected to address the specific challenges at hand.
Overcoming Design Challenges with Custom Cable Assemblies

1. Space Constraints
In many modern devices and systems, space is often at a premium. Compact designs and miniaturization have become essential, requiring components that can fit seamlessly within tight enclosures. Custom cable assemblies offer a solution to this challenge by incorporating space-saving features such as:
- Smaller connectors and wires: By utilizing compact connectors and thinner wires, custom assemblies can significantly reduce the overall footprint of the cable, allowing for easier integration into confined spaces.
- Flexible routing: Custom assemblies can be designed with flexible routing options, allowing the cable to bend and twist to fit within the available space, avoiding obstructions and ensuring a clean installation.
- Right-angle connectors: In situations where space is limited in a particular direction, right-angle connectors can be incorporated into the assembly, allowing the cable to exit the device or system at a 90-degree angle, minimizing the overall footprint.
2. Harsh Environments
Many applications expose cables to challenging environmental conditions, such as extreme temperatures, moisture, chemicals, or abrasion. Off-the-shelf cables may not be able to withstand these conditions, leading to premature failure and costly downtime. Custom cable assemblies can be engineered to overcome these challenges by incorporating features such as:
- Ruggedized materials: Custom assemblies can utilize materials that are specifically designed to resist environmental hazards. For example, cables can be jacketed with materials that are resistant to abrasion, chemicals, or UV radiation, ensuring long-term reliability even in harsh conditions.
- Sealed connectors: To protect against moisture and dust ingress, custom assemblies can incorporate sealed connectors, which create a watertight barrier around the connection point.
- Shielding: In applications where electromagnetic interference (EMI) is a concern, custom assemblies can include shielding to protect the signal integrity of the cable. This is particularly important in industrial settings or in close proximity to other electronic devices.
3. Specific Electrical Requirements
Different applications often demand specific electrical characteristics from the cables used, such as voltage ratings, current carrying capacity, or signal impedance. Off-the-shelf cables may not offer the precise electrical specifications required, potentially leading to performance issues or safety hazards. Custom cable assemblies can be designed to address these challenges by incorporating:
- Appropriate wire gauge: The gauge of the wire used in the assembly can be carefully selected to meet the specific current carrying requirements of the application.
- Insulation materials: The insulation materials used in the assembly can be chosen to provide the necessary voltage rating and dielectric strength.
- Impedance matching: In high-speed data transmission applications, custom assemblies can be designed to match the impedance of the connected devices, ensuring optimal signal integrity and minimizing data loss.
The Benefits of Custom Cable Assemblies
Beyond overcoming specific design challenges, custom cable assemblies offer several additional benefits:
- Improved reliability: By addressing the unique needs of each application, custom assemblies can significantly improve the overall reliability of the system.
- Enhanced performance: Custom assemblies can be optimized to deliver the best possible performance in terms of signal integrity, power transmission, or data transfer rates.
- Simplified installation: Custom assemblies can be designed with features that make installation easier and more efficient, such as color-coded wires or pre-terminated connectors.
- Reduced costs: While custom assemblies may have a higher upfront cost than off-the-shelf cables, they can often lead to long-term cost savings by reducing downtime, maintenance, and replacement costs.
Case Studies and Expert Insights
The effectiveness of custom cable assemblies in overcoming design challenges is evident in countless real-world applications.
- Medical Devices: In the medical field, where precision and reliability are paramount, custom cable assemblies play a crucial role. These assemblies ensure seamless connectivity between various medical devices and sensors, even in challenging environments like operating rooms or MRI suites.
- Aerospace and Defense: In the aerospace and defense industries, custom cable assemblies are essential for meeting stringent performance and safety requirements. These assemblies can withstand extreme temperatures, vibrations, and shocks, ensuring reliable operation in critical applications.
- Industrial Automation: Custom cable assemblies are widely used in industrial automation systems to connect sensors, actuators, and controllers. These assemblies can handle high currents, resist harsh chemicals, and withstand mechanical stress, ensuring uninterrupted operation in demanding industrial environments.
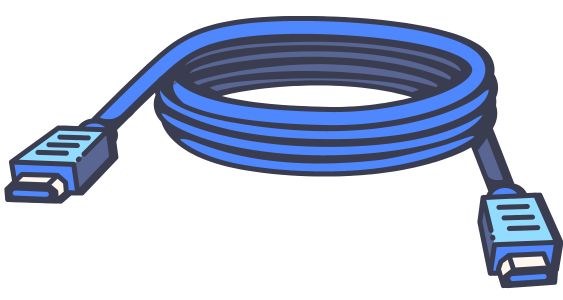
Experts in the field also recognize the value of custom cable assemblies. According to a recent survey by Bishop & Associates, a leading market research firm, “Custom cable assemblies are increasingly being adopted across various industries to address specific design challenges and improve overall system performance.” The survey further reveals that “The market for custom cable assemblies is expected to grow significantly in the coming years, driven by the increasing demand for miniaturized, ruggedized, and high-performance cable solutions.”
Conclusion
In the ever-evolving landscape of engineering and product design, custom cable assemblies have emerged as an indispensable tool for overcoming a wide array of challenges. From space constraints and environmental hazards to specific electrical requirements, these tailor-made solutions offer a perfect fit for unique applications. By incorporating innovative features and utilizing carefully selected components, custom cable assemblies can improve reliability, enhance performance, simplify installation, and reduce costs. As technology continues to advance and design requirements become more complex, custom cable assemblies will undoubtedly play an even more critical role in shaping the future of innovation.
See Also: Circulating Heaters: Essential for Efficient Fluid Heating